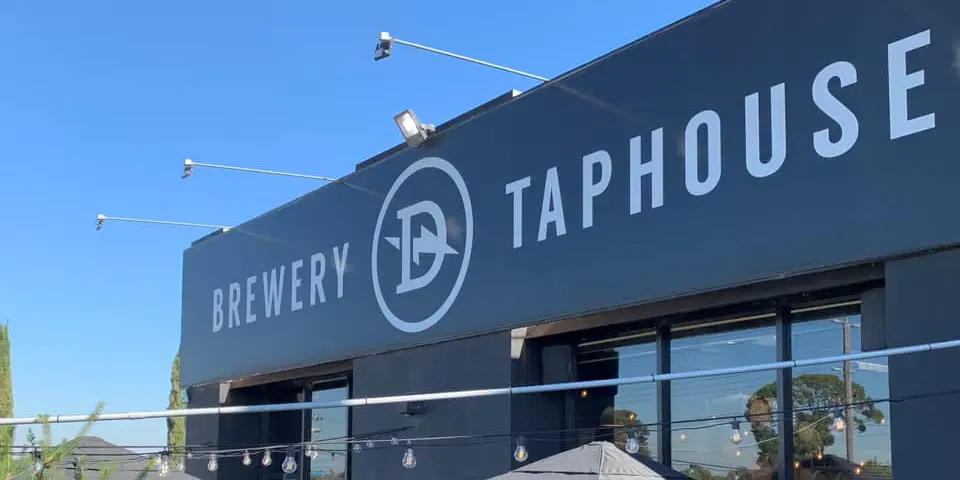
Sustainability initiatives in hop production
Welcome to this BreweryPro podcast looking at quality assurance in hop production, part of Hop Product Australia’s 2021 Virtual Harvest program.
In this episode, HPAs Simon Whittock gives a presentation on HPA’s latest sustainability initiatives. He discusses how HPA considers the economic, environmental and social impact of every decision, and are taking shared responsibility for a better world by setting meaningful sustainability targets.
Stay tuned for a special Q and A with Richard Adamson, Non-executive Director at Young Henrys Brewery. Richard is a champion of sustainability. He started with a homebrew kit over 20 years ago, and now his beers are enjoyed in bars and backyards around the world. He’ll be answering questions about his latest sustainability initiative – the Algae Project. If you’d like to skip straight to the Q and A, jump ahead to 12:50, or to just skip to the next chapter in your app.
A full transcript of this podcast is available below or can be downloaded.
TRANSCRIPT
Sustainability initiatives in hop production
Simon Whittock: Hi, I’m Simon Whittock, Manager of HPA’s Agronomic Services Department. Thanks for taking the time to learn about our sustainability initiatives.
Over the last couple of years, we’ve been able to allocate more resources to this very important area, and we’re excited to tell you all a bit more about it. I think it’s important to say that a lot of this work has been collated by George Webster in the last 12 months, and he couldn’t be with us today so I’m subbing in for George.
As the largest hop grower in Australia, it’s important for HPA to consider the environmental, economic, and social impact of every decision we make. We are committed to improving our business practices based on the Corporate Social Responsibility Framework set out in the Global Reporting Initiative Standards.
HPA, as a regional representative of the broader BarthHaas group, is also a participant in the UN Global Compact, which we use to evaluate our business operations, manage risk, and identify opportunities for corporate responsibility regarding global issue of human rights, labour, environment, and anti-corruption. We use the UN Global Compact, global reporting initiative standards, and opinions of internal and external stakeholders to create a materiality matrix of our environmental, economic, and social responsibilities for growing sustainably.
At the end of this year, we intend to publish our initial report on our sustainability initiatives in relation to the key metrics identified in the materiality matrix. A key criterion that we are reporting on will be our employees, community engagement, stakeholder dialogue, resource management, and suppliers and customers. These criteria are based on HPA’s core values and objectives with input from the broader BarthHaas group.
HPA promotes a healthy company culture through social events, internal policies, and a vested interest in the mental and physical health of our employees. We comply with all state and federal regulations, including statutory inspections, safeguards, danger signals, controlled handling of dangerous substances, measures against dangerous work, and compliance with protective equipment to ensure everyone returns home in the same state they arrived in.
HPA ensure fair business practices are observed as they provide the necessary framework for remaining vigilant against competition law violations, insider trading, price manipulation, conflicts of interest, and systems for responding to complaints outside the company. We have also installed a whistle-blower policy that protects people who report wrongdoing, either internally or externally. This document can be found on our website.
HPA have developed enterprise agreements for farm employees in accordance with the guidance of the Australian Fair Work Commission and the relevant union representation. This provides better quality of life for our employees, as well as better socioeconomic outcomes for families and communities. We are also committed to employee development and career advancement, ensuring that opportunities such as training and promotions are provided equally, and we are continuing with COVID Safe plans this year, which is the reason why we are bringing the farm to you through a Virtual Harvest.
At HPA we aim to be a positive presence by engaging with local events, volunteer groups, and sponsorship of sporting clubs including, but not limited to, the Bushy Park Show, Myrtleford Festival, Bushy Park Fire Brigade, Ovens Robin Fire Brigade and Rotary, all of which enrich the communities in which we operate.
HPA always carries out farming operations in a way that is mindful of others who live and work in the area. We also support the development of our local communities with job creation, skill development, and priority purchasing of local products and services from businesses such as EE Muir, Tafco, and Alpine Mapping to name a few. HPA has also worked with local councils and community groups to improve shared resources, protecting the health of our waterways and the biodiversity hotspots that fringe our farms.
The customer experience is fundamental to our strategy for sustainable growth. We can enhance this experience by always being aware of the environmental impact, social impact, or impact on customer products. We are happy to share information about the standards our products are held with our brewing customers. HPA also ensure the quality and safety of our products are regulated through a mix of audits and third-party accreditations. Our Virtual Harvest session on Quality Assurance goes into the certificates, policies and statements listed on the right in more detail, and they’re also available on our website.
HPA maintains active memberships with relevant industry bodies to stay current and contribute to the discourse and new developments. We’re members of the American Society of Brewing Chemists, or ASBC, that helps improve and bring uniformity to the brewing industry on a technical level. The Independent Brewers Association Australia, or IBA, that helps build a strong, sustainable future for our industry under the vision of quality independent beer. The Institute of Brewing and Distilling, or IBD, that helps advance education in the sciences of brewing, fermentation, and distilling. The Australian Sustainable Agricultural Initiative, or SAI, provides practical and commercial perspectives on issues and policies that impact the agricultural sector and food and beverage production in Australia. Sedex, which is a third-party auditor that improves management of supply chains in line with the UN Global Compact and Global Reporting Indicators. And the UN Global Compact that ensures corporate responsibility, including vigilance against corruption in all its forms. The Sedex auditing program provides transparency and preserves human rights throughout our supply chain.
HPA source the most environmentally friendly packaging whenever and wherever possible. Our suppliers meet the Australian standard for sustainable forests, timber and paper, and Forest Stewardship Council Certification. We also contract third parties to collect our reusable waste streams. Recycal collects scrap metal, TerraCycle collects our single-use plastic, specifically gloves that are used for lab analyses. And Ag Safe Products Stewardship Program collects our empty agricultural chemical containers.
We employ various methods to manage soil health on our farms. Cover crops, predominantly cereal rye grass, are used to improve soil health. We also undertake annual soil tests to establish nutrient levels, which inform future fertiliser applications.
Water management is becoming increasingly important with the changing climate. HPA use in-field probes to continuously monitor and report soil moisture levels, which ensures our irrigation systems are working efficiently and effectively. We continually assess our irrigation needs using climate data, moisture probes, and crop surveys during critical growth stages.
In Victoria we’re planning for an additional 300 million litre dam that will help protect the flow of the Ovens River, which also sustains local flora, fauna, and recreation. And in Tasmania we’ve worked with local council groups to manage and restore biodiversity of the riparian zones on farm.
HPA recently replaced all our metal-halide lights that contain dangerous heavy metals with LED lights that are far more energy efficient. This has reduced our power consumption by 68% and our Carbon Dioxide emissions by 220 tonnes across our farms each year. The largest drop was in Victoria, where the primary source of electricity is derived from coal, compared to Tasmania where the primary source of electricity is hydroelectric.
HPA engaged an environmental consultancy firm to perform an on-farm energy assessment as part of the Agricultural Energy Investment Plan funded by the Department of Jobs, Precincts and Regions. The AEIP support farmers in identifying and implementing energy efficient opportunities with the aim of building greater energy resilience in the agricultural sector. It focused on farm energy use trends and also included a pre-feasibility study for switching from LPG to a less carbon-intensive fuel for the purpose of drying hops.
This graph shows the energy consumption breakdown for our Victorian farm. LPG is the major form of on-farm energy consumption, contributing 67% of overall energy needs. The next-most energy intensive operation is irrigation, contributing 23% of overall energy needs across a mix of diesel and electric irrigation pumps. Therefore, the key areas identified by the report in which operating efficiencies could be gained are from the modifications or upgrades to electric irrigation pumps, installation of drippers as the primary source of irrigation, or kiln heat recovery during drying.
The development and deployment of Near Infrared analysis has been a key project for our Department of Agronomic Services over the past three years. NIR analysis allows us to reduce inventory and handling of potentially harmful and highly flammable solvents, which will improve occupational health and safety in our labs, as well as reduce waste production.
Our team partnered with Data Science Company SAGITTO to build the predicted models using spectrophotometric data. Near Infrared analysis has significantly reduced our need for solvent analysis of pre-harvest maturity, bale condition, and our experimental varieties, and has already resulted in a reduction in our Tasmanian labs solvent stock, as shown in the graph on the left. It has also resulted in a reduction in Carbon Dioxide emissions associated with the production and disposal of solvents, as show in the graph on the right.
The success of NIR analysis has allowed us to eliminate lead conductance value titration, an outdated industry standard methodology, from our lab operations. This is a great result since lead has long been known as a highly toxic metal that also has the potential to contaminate soil and waterways.
HPA’s Agronomic Services division has been established to provide the company with a better connection between our hop breeding program and our horticultural practices. It will also oversee the performance of our labs in terms of crop monitoring and analytical procedures. The Agronomic Services division will be the lead on identifying and delivering sustainability projects, and key information will be fed to management to inform good decision making and facilitate uniform procedures across our farms in Victoria and Tasmania.
HPA’s hop breeding program is a key element in the sustainability of our business. We prioritise unique flavours in the development of new cultivars, only select those that display high stable yield over time, as these are the plants capable of thriving in a commercial context. The aim is to maintain a diverse catalogue of experimental varieties so that we can introduce hops to the market that can meet the changing need of domestic and global brewers.
Thanks for listening, and please stick around for the live Q & A featuring Richard Adamson from Young Henrys Brewery based in Newtown, Sydney, New South Wales. And thanks to George again for pulling all this information together.
Owen Johnston: I’m Owen Johnston, head of Sales and Marketing here at HPA, and lucky enough to be joined by two legends. Firstly, I’d like to introduce Richard Adamson from Young Henrys, g’day Richard.
Richard Adamson: Hi all the way from my kitchen in Sydney.
OJ: Richard is non-executive Director at Young Henrys, his passion for beer started from a home brewing kit over 20 years ago. I first started hearing about Richard in his adventures at Barons Brewing from around 2005. Richard went on to start Young Henrys in 2012 and added a distillery in there and really became quite well known for things like collaborations with the Foo Fighters, Kylie Kwong, one of our local chefs, and the Art Gallery of NSW.
They’re also industry leaders in sustainability, and Richard was really top of mind to me to reach out to and see if I could get him to contribute some of his great knowledge to this segment for us. Richard’s going to talk about some really interesting stuff a bit later on.
Thank you, mate, thanks for joining us to contribute.
RA: My absolute pleasure.
OJ: And, of course, Dr. Simon Whittock, head of our Agronomic Services Department and leading up our breeding program here at HPA. Simon, thanks mate, it’s still middle of harvest for us so I appreciate you making even more time for us.
SW: Back again, OJ, thanks.
OJ: First let’s kick off with a couple of questions to Simon.
For HPA, addressing sustainability in this way is reasonably recent; can you tell us why did HPA sign up to the UN Global Compact?
SW: Thanks, OJ.
We have had an interest in pursuing sustainability goals for some time and at some point a few years ago this coincided with the global BarthHaas group looking for a procedure by which to pursue sustainability goals, and in that conversation as a global group we decided to focus on the UN Global Compact to give us our guidelines and reporting structures. From there it was HPA, BarthHaas group, choosing Global Compact and making a commitment through that to, one, fulfill the reporting requirements, and to set the goals and try and achieve real outcomes on the ground.
OJ: The BarthHaas group and the related hop-trading entities around the world, this is BarthHaas Germany, BarthHaasX in the UK, HAAS in America, HPA out this way, this ends up constituting quite a significant undertaking for a reasonable portion of the world’s hop-trading. For me, it’s a really meaningful step for the BarthHaas group of companies to go down this path.
SW: Yeah, sustainability’s a large, complex problem, so you can either approach it piecemeal and try and achieve small outcomes in your own right, but you really do need that structure and those reporting guidelines to guide you as to the other things that you should actually pay attention to. And Global Compact particularly focuses on human rights and labour rights, things like that.
OJ: Moving away from the Global Compact, water is always a pretty hot topic in farming, generally, coupled with issues around climate change. What are we doing to make sure we manage water responsibly and have an appropriate amount of water?
SW: Our pre-existing farms in northeast Victoria and Tasmania, the land they are situated on is associated with access to environmental water in those areas where we’re fully irrigated. It’s really incumbent upon us to be responsible with how we use that water.
During our expansion we’ve made sure that the land we’ve expanded on to has access to water, and we’ve also committed to a process of, particularly in Victoria, building appropriate dam storage to allow us to take winter offtake from the rivers and store that primarily as an emergency backup so that we don’t have to access the rivers at inappropriate times like in droughts or in flood events or bushfires or things like that.
OJ: Just for some context there, all of our farms literally border quite major local rivers. Unlike some growing regions around the world that are not irrigated, we have that advantage, luxury, but also responsibility. Adequate water rights plus appropriate water management.
SW: Hop growing in Australia has always relied on irrigation, and for us it’s a matter of being responsible about it and getting better at that management so we’re only using exactly what we need to use to produce a good quality crop.
OJ: If you want to hear more about, or see more about our growing regions, jump on the hops.com.au website and there’s a little bit more about the locations and some of their attributes.
One of the other hot topics, so to speak, in sustainability is around energy and around the assessment of energy. It’s pretty obvious, you would say, that we consume quite a bit of energy through the kilning process and there is a lot of energy lost as heat through that process. It seems like a hot topic.
SW: That’s your favourite line, isn’t it, OJ? Gold when you find it.
Hop production is undeniably energy intensive. The actual horticulture’s an intensive horticulture, and the drying is energy intensive. There are alternative energy sources for hop drying in use around the world, and there are alternative kiln structures in use around the world. That energy assessment report that we participated in identified kiln heat recovery as a potential way to ameliorate the energy intensiveness of our kilning operations.
That’s well and good in theory. It sounds obvious, but when you have an existing kiln structure, the engineering required to make that safe and viable obviously comes at a cost, and we’re not at the point now where we can make that evaluation and that commitment that that is the right solution for us.
OJ: Are there other systems around the world that have succeeded in that challenge, that you’re aware of?
SW: I don’t know that I could answer that question precisely, but when you have a louvered kiln and you’re controlling the output, the humidity of the output air and things like that, you have a better opportunity to recirculate. Typically, they’re a smaller-scale operation.
OJ: But in no sense have we seen a closed-loop system where there’s energy regeneration?
SW: Not that I’m aware of.
OJ: So there might be some re-use and re-circulating of heat energy in certain kiln designs, but it’s not by far…
SW: And I’m really not the right person to talk to about the engineering of hop kilns.
OJ: You’re a lot better at it than me.
Alright, back into something that maybe is closer to your heart, the role of the NIR analysis that we have been talking about quite a bit through this program.
Can you tell me how the application of this technology is helping to driveour sustainability?
SW: There’s two major ways, the first one is just in outright solvent use. When we use solvents, which we are obliged to if we’re following the industry standard analytical methods for hop acids, we use a lot of toluene, a lot of methanol. We have to handle those safely, we have to minimise exposure to our staff, we also have to dispose of those solvents safely once we’ve used them. The way that we have taken on NIR into the business as an integrated into our process control systems we’ve drawn down our solvent use on each of our production sites, from about 600 litres of solvent per year on each site to maybe 60 on each site, and still going down as we find more ways to use that NIR system.
In terms of Occupational Health and Safety, or staff wellbeing, welfare, and the solvents in the environment, they’re small-scale wins, but they’re a big win in terms of that process.
OJ: Absolutely. I would say they are two of the major criteria that we would seek to address, is our environmental impact and the safety and wellbeing of people.
SW: That’s right, they’re two of the criteria front and centre of the Global Compact.
OJ: We’ll we’ve heard a little bit more from Simon about the journey that HPA has been on, but let’s hear from Richard.
Before we get into it, Richard, you, in fact, teach on the topic of sustainability. Can you tell us a little bit about that?
RA: It’s one of the many topics that I teach. I’ve been teaching Certificate III in Food Processing and Brewing for five years at Ultimo, and sustainability has to be one of the topics delivered. I’ve done some research in the field, not just for what Young Henrys is doing but just to be able to talk about it a bit more broadly as well.
OJ: That’s fantastic. For my gratification, the guys coming out of your Cert III in Food Tech, they’re finding readily useful skillsets and getting jobs in breweries?
RA: They certainly are. The first year we had 100% of students get work in the industry. Even through the COVID lockdown of 2020 we managed to deliver the course. We moved to this environment of Zoom that we’re all familiar with now and got most of it done. Most of those students are working in the industry, and I’ve seen a big uptick this year, we’re already getting enquiries through TAFE for skilled hands, or even just people starting the course. The demand for qualified brewers is still high.
OJ: I would say that that trend will continue as we’re still seeing – maybe it’s taken a bit of slowdown over COVID – but I’d say we’re still getting a new brewery every week here in Australia. The requirements for skilled hands on deck is still coming along.
RA: It is, and we’ve been through the IBA, we’ve managed to get TAFE in Queensland to deliver the course there. Our rockstar, Hendo, has been teaching there this year, I think he’s had his first bunch of students through, and they managed to pick up a silver medal at the local awards there, which is fantastic. And South Australia have been running a pilot program for trainees as well. We’re hoping to get WA and Victoria over the line very soon.
OJ: That’s fantastic. I did see the silver from Hendo and his team, so good on you guys, well done.
Alright, back to the Young Henrys story of sustainability, I’m pretty sure that I’ve never come across a brewery starting up with a sustainability matrix buried in the business plan, so I feel like we’ve spoken about the journey that HPAs on, but I think it’d be fair to say we’re all on a sustainability journey.
Can you go behind the scenes at Young Henrys for me and share some of the journey?
RA: Absolutely. We’re still on it, we’re by no means experts or perfect in this field, we’ve got a long way to go, ourselves. But I guess it started, for us, with the growlers, having a 2-litre returnable bottle. When we were beginning it was our only means of packaged product, and when you look at the impact of what reusing glass can have as opposed to recycling or not recycling has an exponential impact on your carbon footprint. That sparks your interest from there in seeing what else you can do.
From there, we had a few things happen that were very fortunate. One was we got approached by Pingala, a community run solar project. They were interested in putting solar panels on our roof, which meant we didn’t have to stump up for the capital investment initially. We lease the solar panels on our roof, Pingala offer shares in that solar panels to the community and they bought in and it was community funded. They make a return on their investment, and we get solar power at a much-reduced rate. So that’s about 25% of our energy and we’re about to kick that up to 50% with another Pingala project to put solar panels on the other side of the brewery, which is going to be great.
At the same time, we went for a high-efficiency brew house with the mash filter which reduced our water use and how much grain we have to use, as well. That was two big steps we went towards sustainable Young Henrys.
OJ: It’s interesting that dovetail between, what would you say? Commerciality and cost-effectiveness, and where it works in harmony with a sustainability initiative, and I think that community piece and the solar panels is absolutely fascinating and would expect to see more of that down the track.
RA: I think so. Not everyone in the city can necessarily participate in solar energy generation. If you’re leasing or if you’re in a block of flats or something, you can’t necessarily put solar panels up. Being able to get on board with a community project and provide solar energy production for industry is a really good thing.
OJ: Fascinating. You mentioned the mash press as an efficiency step and a reduction in grain as a material input. How do you conceive of and deal with raw materials from a sustainability point of view?
RA: Every step you can make to reduce waste and use less is going to have an impact on your sustainability, and your bottom line as well. I think where we look at it, and from our research one of the biggest carbon costs is transport, so if you can reduce your carbon miles for any of your ingredients, it’s going to go a long way towards your sustainability goals. Using hops that are locally grown does go a long way towards that.
OJ: Is it useful for you, as a brewer pursuing your own sustainability credentials, that HPA is a signatory to the UN Compact and we have active reporting on this stuff. Is that useful?
RA: 100% it is useful. We’re relying a lot on our suppliers to do the heavy lifting when it comes to sustainability because beer is an agricultural product. We’re nothing without the hops and the grain that goes into the beer, and if it starts at the farm, we’re already ahead, so it makes a huge difference to us.
OJ: Excellent, excellent. It’s always nice to know that what we’re doing makes a difference.
I feel like you guys have gone one step further and I’d like to explore the Algae Project with you because I think this is a really cutting-edge sustainability initiative. Can you talk to that?
RA: Absolutely. A few years ago, I was invited to UTS, the Climate Change Cluster, C3, and had a look at what they were doing in the algae space. I was fascinated by these green, glowing vats that they were all working on, it looked like something out of some sort of Sci-Fi movie.
But also, that yeast had this analogy with algae in that it almost felt like they’re sisters and they do the opposite job. Yeast is taking in sugar and producing CO2, alcohol, obviously, and algae is taking in light and CO2 and producing sugar. Basically growing. I thought if we could get those two things into some sort of equilibrium or balance, you could have a closed-circuit system within a brewery, and then we could look at what uses the algae could have beyond that and if we could then use the algae for the carbon reduction or just producing a product that was then going to go and have another use, then we have something that’s very interesting. And that was what kicked off the research from there.
OJ: Forgive my ignorance, where does the algae – I assume it’s like yeast in a tank, you end up with a great biomass – does that go out to animal feed or something like that?
RA: Algae has so many different uses. Where the research is focused on now is what that next use is going to be. You’re right, animal feed is certainly one. Humans can eat it as well, so there’s been a fair bit of work on supplements for humans. It’s very valuable as a medium for pharmaceutical manufacturing, and obviously wastewater treatment is the other.
The good news is that in all cases it needs CO2 to do its job, so if we can capture and reuse the CO2 within the brewery, but also the brewery produces more CO2 than you need, put that excess into growing the algae, it’s possible we could get to a neutral or net negative outcome.
OJ: The blue-sky opportunity here is, even on a big scale, a brewery’s own CO2 demand is always going to be exceeded by its CO2 production from ferment. Do you think the technology will get to a point where a brewery might be CO2 neutral?
RA: That’s certainly the aim, particularly if we can get further reductions from using the algae afterwards. I think microalgae is a really fascinating little beast. Half of the oxygen that you breathe in comes from algae. One of the fascinating stats was the metre-square footprint in the brewery that we have the algae vat growing was producing more oxygen than if the entire site of the brewery was Australian bush.
OJ: Isn’t that fascinating? That’s just fabulous. I was a little bit scared about that statement about half the oxygen I breathe comes from algae. I hadn’t really thought of that.
RA: Yeah, it’s biomes in the sea that’s producing most of the oxygen.
OJ: That is very true.
What else would you like to tell us on the story about Young Henrys journey?
RA: Probably the message to anyone that’s thinking about it is, you have to measure to understand what you need to control. When you start looking at that, it can be very daunting. You’re looking at energy, agriculture, CO2 production, your packaging, distribution, water, you could potentially freeze up at that point and say it’s all too hard. I think it’s about taking baby steps and see what the quick wins are to start with, and then working through it slowly and methodically. Doing something towards this rather than nothing is always going to be a positive step.
Do what you can within your capacity and keep working at it.
OJ: That’s exactly right, that’s pretty much how we approached it. Bit by bit.
Finally, Richard, probably the biggest question as the last one, what do you see in the future? Where are we going? And this could be a national perspective, it could be down to the microcosm of the brewery, what’s piquing your interest? Where do you see the future lying?
RA: Great question. I think Australia as a nation is in a pretty challenging part at the moment for energy production overall and a sustainable path. The coal-fired power stations won’t be affordable in the future. We’re seeing a lot of energy-generators saying that they’re hoping to close them down sooner rather than later. Gas, I think, as a source of energy in Australia, I think the easy gas will disappear. We’ll have to be looking at fracking and all the rest of it, so as a transition I think it’ll be useful, but long-term it won’t.
It’s about having the infrastructure for renewable sources, and that’s in that high-power transition between the states and its storage of energy.
OJ: I think it’d be fair to say that change is in the energy mix nationally, part of the national conversation, and they’re certainly on our radar as something that could potentially impact HPA.
SW: Carbon report shows that very clearly.
OJ: Indeed.
RA: It may even be that we have to look at how we generate our own electricity more and more, and how we manage that. Having a picture of what draws energy on your site and how you can maybe look at time of use and things like soft switches for refrigeration. It’s an overall management, it’s not just as simple as plugging things into the wall now.
OJ: But some of those techniques are available today, such as the soft start to avoid those spikes in power draws on significant kit. they’re available. Even co-generation, there are some examples globally of breweries using co-gen, what do you think about that? Are there barriers to that here in Australia?
RA: I don’t think so, no. You’re right, a lot of these technologies are here, and we’ve implemented some of those things we’ve talked about, like soft switches. I think the impetus to do so will become more prevalent, though. These things are available, I think there’s a fear of cost and hassle, but I think those things will become part of an operation that you’ll have to consider these things. And I think from a cost level you’ll find that it’s actually going to be cheaper in the long run.
OJ: Certainly, if the cost of energy per kilojoule goes up, the ROI becomes a bit more compelling. But there’s also potentially the old legislative big stick where the community is heard, and people have to start taking this stuff seriously in that way.
RA: I think so, and if you look at what’s happening with the UN looking at products like steel, the energy used to make steel will have to come from a sustainable source, otherwise there’ll be a tariff on it. You may even see that across all products, so you guys getting on top of this now as a farmer and a producer of hops, if you’re looking to export into Europe, that may be a requirement that you have all this reporting. It’s good to get ahead of it now.
OJ: Absolutely, and I liken it to MRL legislation over in Europe, for example. If a jurisdiction starts bringing in criteria by which you are deemed not suitable to sell your product in their market, we need to be very conscious of that. This is this interface between commerciality and sustainability. It’s a pretty important topic.
RA: It’s that old triple bottom-line accounting that was floated a while ago, those bottom lines will become one. You’ll have to do it.
OJ: Good luck untangling them.
SW: The other comment I’d make there, too, is we’ve been reading for a long time about modelling suggesting that market-based mechanisms are preferable, more efficient in these things, but the reality is those marked-based mechanisms haven’t got up and running. The legislative side of things, I think, is going to come.
OJ: It’s market-based or it’s, for want of a better term, it’s actually self-interest from big corporate actually making decisions that make sense.
SW: I think there’s been so much inertia it’s getting to the point where those market-based mechanisms are going to be recognised as not having done enough and we will see legislation come in.
RA: I think as industry leaders and as businesspeople, we do have to take leadership in this role. We can’t rely on government to do everything for us.
OJ: I don’t think you’ll find any disagreement with that statement here.
Richard, thank you very much. Simon, thank you very much. Let’s wrap up the conversation there. Again, quite a fascinating topic for me. Richard, thanks very much for your insightful commentary and sharing some of that experience that you’ve got on your journey. Simon, thanks for shedding some light on the HPA journey, and I think it’s fair to say that both of our companies are going to continue to pursue this.
RA: Absolutely, my pleasure guys. Glad to hear harvest is going well.
OJ: Fingers crossed, we’re pretty close to the end of the March 2021 harvest now, so with a bit of a fair breeze we’ll get over the line.
RA: Catch you guys later.
OJ: Alright, thanks very much.