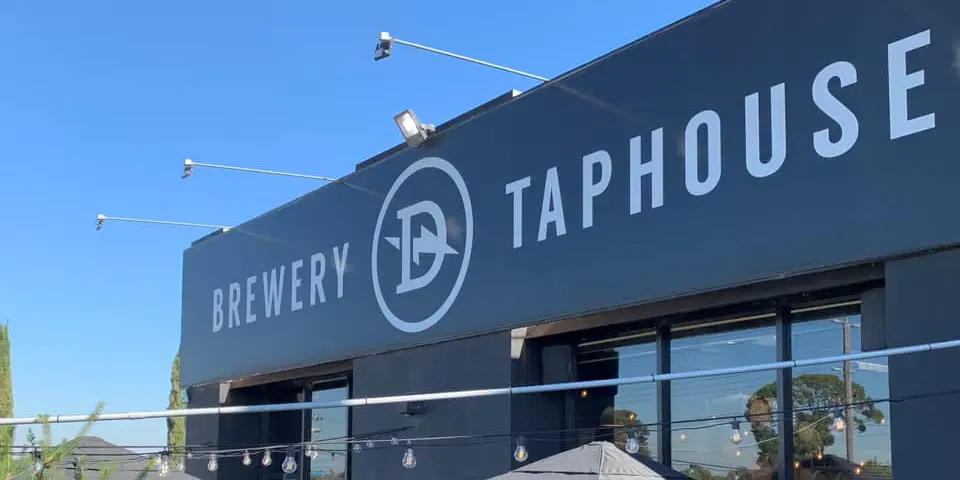
Suppliers resilient in face of COVID-19
Brewing industry suppliers have taken the front foot and are showing resilience in the face of the COVID-19 pandemic.
Ingredients and packaging suppliers are amongst those that are reassuring brewery customers that supply is secured, and for most, there will be minimal disruption at this stage.
Advice has been to prepare as early as possible to make orders, and to get in touch with representatives if there are any issues.
We spoke to a number of brewing industry supplies for updates and advice.
East Coast Canning
Chris Kelly of East Coast Canning reassured customers that the business has enough supplies and its suppliers remain open, and their work in the FMCG sector means they are likely to remain so.
“We are busy, as we are the only mobile canner in the country that can package from kegs, and we are pushing hard to help people left with stock,” Kelly told Brews News.
He said that East Coast is making its machinery available for afternoon shifts almost every day, including Saturdays. The team will also be available to help customers with deliveries, direct to customers or wholesale.
“I also believe that once the backlog of keg stock and beer-in-tank destined for kegs is packaged and out to consumers, we will be left with a new understanding of what consumer demand for packaged beer looks like in the face of venue closures,” he said.
“My opinion is that we will see a strong winter of packaging beer into cans provided people continue to support local, and our industry remains open.”
In terms of advice to brewers, Kelly said that if ’Keg is King’ then taprooms are palaces.
“What brewers need to do is reach out to everyone who visits their palace, and get them to repeatedly buy packaged stock.
“There is a great opportunity for brewers to keep their tap room customers drinking their product through packaged takeaways, online orders, beer clubs, online brewer sessions, and a host of other creative initiatives. I guess quite simply – there is a pivot required!”
Find more information on East Coast Canning’s website.
Bintani
Ingredients supplier Bintani shared an update with customers last week confirming that it will continue to supply the industry.
Bintani has all its 2020 hop stock either in cool rooms or en route, with no reported interruptions from international malt suppliers Weyermann, Simpsons, Briess or Gambrinus, or Joe White, which produces domestically.
Bintani company Fermentis has reported that production is currently continuing as normal, and the business is increasing stock levels to mitigate any potential supply interruptions.
It said that all sites are in operation, and working to the “highest practical standards” of hygiene.
However it did acknowledge that international freight, particularly by sea, had seen some disruption. Bintani said that there was a reduction in the number of vessels moving cargo, which may result in longer delivery times in some instances, although the company said the situation has so far stabilised at a manageable level.
Within their business, Bintani is segregating its business into teams to eliminate contact and transmission within the business at its eight Australian and two New Zealand warehouses, with many staff working from home where possible.
“Having our ingredients located in 10 different locations we feel we are well placed to deal with the increasing infection numbers whilst ensuring business continuity,” the update said.
“We have been serving this industry for 25 years and been through thick and thin with many of you before and we are confident by working closely together we will get through this current crisis.”
Find out more on Bintani’s website.
Hop Products Australia
Owen Johnston ofHop Products Australia told Brews News that the company is doing everything it can to guarantee supply.
“The two most important things to us are the health and safety of staff, and the outcome of our harvest which is underway right now.
“From our point of view, those are hard to separate, but we have taken action and are closing the farms to all non-essential staff.”
In terms of casual staff, Johnston said they were lucky in that they ramp up employment of casual staff towards the end of the year, so they will not be affected at this stage.
“We very strongly believe we will get through this and get the crop in, and we’ve been working with additional, freight and cool store operators, so we’ve got contingency plans in place and are using a spread of cool stores.
Johnston said that in terms of order fulfillment and short-term concerns, HPA had split its workforce in half, alternating from working from home and the office, as an insurance against the team falling ill.
“But we’re business as usual in the sense that its order in, order out.
“There is no interruption to supply at this stage because the harvest will come in on track.”
While everything is business as usual from HPA, Johnston said that brewers should be aware that while trucking companies are still functioning, HPA’s fulfilment team is navigating the nuts and bolts of getting stock out the door.
Freight companies are bringing in measures including contactless deliveries.
“And we’re very happy to get on board with that, an at this stage, I’ve got confidence we can keep orders going out the door.”
“From my point of view, as a face between agricultural pursuits and the brewing industry, I’m really feeling it for the brewers with the hospitality shut down and decline in on-premise sales. It’s not like we will be immune from that as a supplier.
“I’m hoping the volume gets displaced into off premise – and it’s every beer drinker’s civic duty to drink beers and keep the industry going!”
HPA will be updating the industry next with the crop report.
Find out more on HPA’s website.
Cryer Malt
In an update to the Cryer Malt website, general manager David Cryer said that the business was “taking all possible steps to provide uninterrupted supply and excellent service” to its customers.
Cryer suggested getting in touch with the company’s sales team, saying that they were aware that cash flow might well be uncertain.
He recommended that brewers build in extra time for all orders to ensure it can arrange transport providers, although Cryer is currently not experiencing service issues with road, post or ocean freight at this stage.
“With Cryer Malt having product stored in four States in Australia and three cities in New Zealand, we are well prepared to support you during this difficult time,” Cryer said.
“In the unlikely event of a warehouse closure, we are in the fortunate position whereby we can supply from interstate to ensure disruption to your business is minimised.
“With the changing nature of the situation, we are carrying additional stock and we suggest you also do so at your facilities, where possible,” he also said.
Sister company Barrett Burston Malting also has three malt houses across Australia which will remain operational during this time to maintain bulk malt supply.
Cryer Malt did announce that visits to malthouses and warehouses have been suspended, and that business travel and customer visits have been limited.
“We understand that you may have further questions or concerns. If this is the case, please contact your local sales manager or our customer service desk for more information,” the team said.