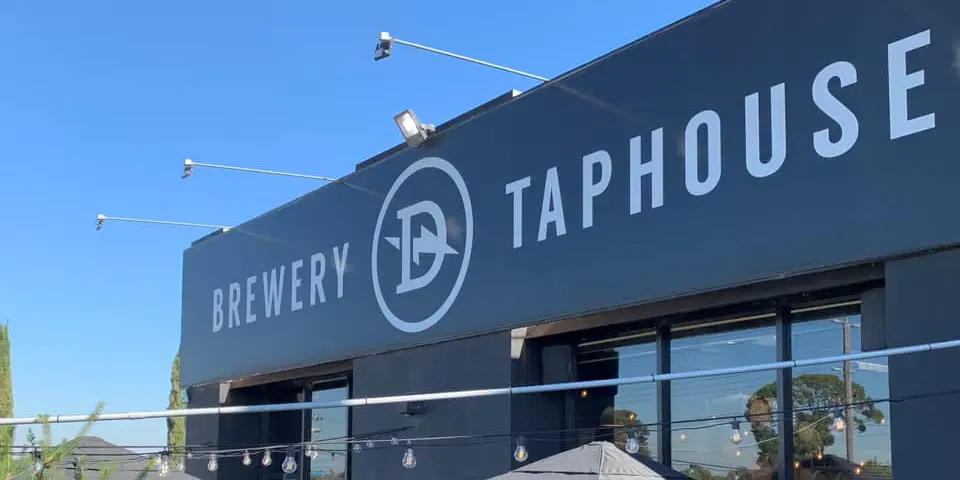
Smaller is better as craft beer booms
As Australia’s craft brewery boom continues, equipment manufacturers are working with breweries to develop more agile, industry-specific technology.
Earle Roberts, Chief Customer Officer for one of Australia’s largest packaging suppliers Foodmach, says that the beer market in Australia has gone through a seismic change, which has resulted in different equipment needs.
Due to the minimum-batch sizes demanded by larger production facilities like CUB’s Abbotsford plant and Lion’s XXXX brewery in Queensland, Edwards said that the bigger facilities struggle to be able to do craft type runs.
This is one reason why more compact and efficient equipment is needed by both the craft arms of larger corporations and medium to large independent craft breweries.
“As a manufacturer, we’re trying to come up with something that’s competitive and attractive for the craft guys given that there’s strong growth in that sector,” Roberts said.
He said that the market shift towards cans has prompted manufacturers to produce more flexible packaging design as adding an additional line isn’t feasible for many breweries.
“The ability to change over from product to product or SKU to SKU very quickly and get back into production as quickly as possible drives efficiencies.”
The only all-in-one or Combifiller design in the world is patented by Slovenia-based manufacturer Vipoll. Edwards said that the Vipoll Visitron case filler is the first in the world to be able to run glass, aluminium and PET bottles through the one machine. He said that it can change from one format to the next in 27 minutes.
Malt Shovel installed one of the new machines in 2018, to make the Lion-owned brewery the first in Australia with the technology.
CUB-owned Pirate Life is another brewery to benefit from new packaging technology, having installed a robot palletiser as part of its project to better integrate its packaging line.
To put these efficiencies into perspective, Roberts estimated that Pirate Life is running at 15,000 cans an hour or 250 cans per minute – 10 per cent of the speed of a big canning line at a larger brewery.
“We’ve tried to keep all of the learnings that we’ve got from running canning lines at 2,000 per minute and 1,000 per minute and then tried to apply them down to where we’re running lines at 30 per minute.”
Roberts said that safety is another huge factor driving equipment manufacturing in the sector.
“That’s something that the true craft brewers I think need to be very mindful of… when it comes to an accident it doesn’t matter if you’re a large multinational or a small operation, the consequences to employees are still the same and the legal liabilities of the directors remain the same.
“A lot of work that we’ve done is just upgrading both our own old equipment and other suppliers’ equipment to current safety standards.”