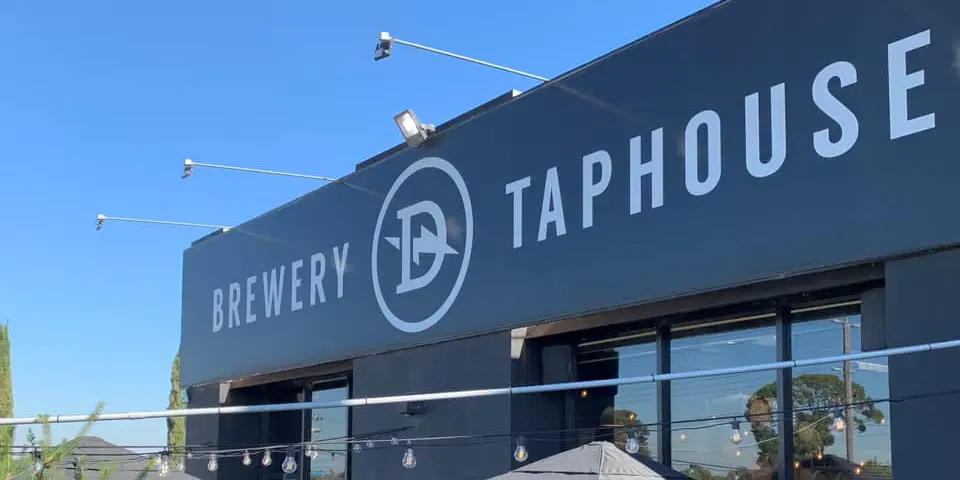
Milling - key considerations you should know
We mill our grain to crush the starchy centre making it and other malt compounds easier to dissolve or extract, utilising our malts internal enzymes. If our malt is well modified and adequately friable we should have no issues milling. The impact on downstream processes that milling influences cannot be underestimated. Thankfully by paying close attention to the gap between the mills rollers and the grain crush, we can be in total control of our process from the first step.
The grain crush influences the trade off between extract recovery (efficiency) and total lautering time. The distance between the rollers is influenced by the mill type, the type of malt and adjunct to be used in the grist, malt quality, your brewhouse equipment and your mash method. The most common type of mill in many small breweries is the two roller dry mill, they are compact, inexpensive and get the job done and will be the focus of this article.
Extract – a quick definition
Malt is a key input in the brewing process. We mill the malt and combine it with water to extract the soluble portion of the malt, this soluble portion is called brewers extract. The water and extract mixture we create is called ‘wort’. Extract is measured in degrees Plato or specific gravity.
Impacts of milling on Process
To ensure effective recirculation, lautering, brewhouse cycle time and extract recovery, milling needs to be under control. The husk of our kernel is very important and forms a filter bed to trap the insoluble portion of our grain during lautering. If we mill too fine we may get a very slow sparge because our husk can not form a porous filter bed and we can exceed our extract target. Milling too coarsely on the other hand has the opposite effect, causing a fast run off with a reduction in extract efficiency. We must make sure the mill gap is set correctly to allow us to achieve our extract target and separate the insoluble portion of our grain from our wort in a timely manner. Practically we can achieve this by dialling in our mill gap over time and recording the setting until a happy medium is found between extract recovery vs run off time. Then we just need to make sure the mill gap is set correctly each time we mill and that the rollers are free from visible wear and tear or damage.
Getting the most out of you two roller mill
Analysing your malt certificate of analysis (COA).
The Kolbach index or total nitrogen vs soluble nitrogen ratio – this tells us the level of modification that has occurred. The higher the value the more protein that has been broken down and the easier we will be able to dissolve our extract. If our value is too low we may have trouble reaching our extract target and if it is too high we may exceed our extract targets. It’s important to ensure the value is consistent between batches so that way we can predict a similar amount of extract recovery from batch to batch. Typical values are between 38-45%. Lower modified malts can contribute larger proteins into our beer which is better for foam but the trade off is less extract.
Friability – this is a measure of how easily our grain will be crushed, we want values over 85% – if the grain is well modified it will be suitably friable and easy to crush.
So we have carefully chosen our malt. It is well modified and ‘friable’, easy to crush and we have worked out our recipe. Now we need to ensure that our extract target is met and consistently achieved.
We do this by ensuring our malt COA for each batch is the same as the last and we set our mill gap. We must ensure the mill gap is checked regularly alongside the crushed grist. If we are brewing and nothing in our process has changed but suddenly our total lauter time and extract is through the roof! Our mill gap probably needs adjusting.
Setting your mill gap. Typically a two roller mill gap is set between: 0.6 -1.4mm. If you are commissiong always start with 1.4mm and work your way down until you have an efficiency and lauter time you are happy with, sometimes it’s best to lose a little efficiency to reduce your brew day! Brewhouses such as the Spark BrewStack, with a dedicated lauter tun, can handle finer grist and therefore a smaller mill gap. You can measure the mill gap using a set of feeler gauges – it’s really that simple. A quick check and adjustment at the start of the week is all that’s needed.
Analysing your crush
The simplest way to assess your grist is by hand. Take a handful of grist and examine it carefully. The kernels should be broken into pieces and be separated from the husks. The Husks should be mostly intact but empty, free of endosperm.
If we wanted to take this one step further we could use a plain sifter for our brewery. This is a great piece of lab kit to ensure consistent milling. A plansifter consists of a series of graded screens which sift milled malt or ‘grist’ and produce a distribution of different particle sizes; the desirable target plansifter distribution is specific to your equipment e.g a dedicated mash lauter tun vs a combined mash and lauter tun.
Why choose Spark:
There are many questions that may come up when you are planning your brewery build. Spark has installed 50 breweries Australia wide and have all the answers. We work closely to support your decisions before, during and long after a project is complete.
We don’t just supply equipment, we deliver profitable operating businesses and every project gets an engineer, project manager and brewer to ensure high quality beer and speed to profitability.
If you want a long term partner not just an equipment supplier – get in touch.