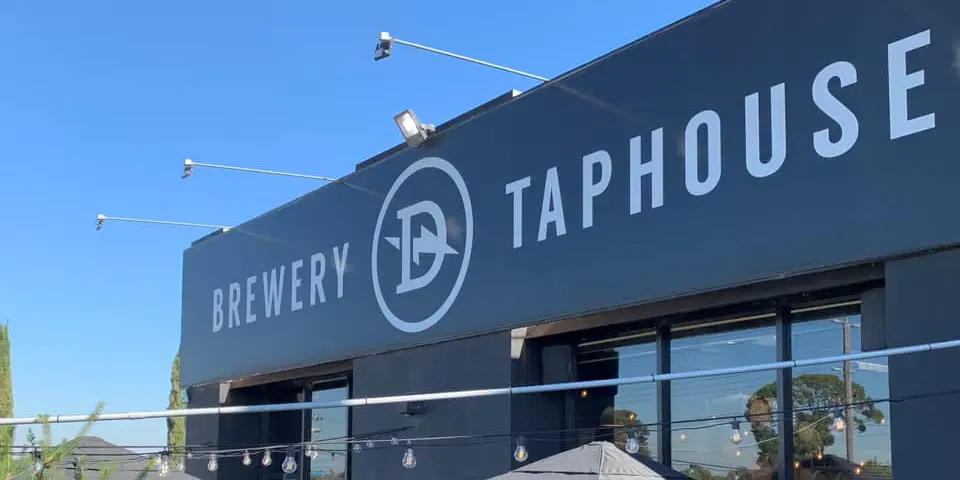
Membrane filtration with Phoebus
In brewing, filtration is the final process step in which the brewmaster can influence a beer’s quality before filling. The process should yield a brilliant, clear filtrate and improved physical stability of the beer. Filtration also achieves a high level of microbiological safety in the filled product. Brewers especially want long-lived filters, low operating costs, and a system that is easy to use. Besides the tried-and-true method of direct-flow filtration, cross-flow membrane filtration has come into wider use in recent years. And now Krones, too, has added this technology to its portfolio.
Combining established technologies and innovation
Steinecker Phoebus is a membrane filter developed on the basis of the Hydronomic UF (ultrafiltration) water treatment system. It integrates familiar mechanical design elements from the Hydronomic UF system that have not yet been used for filtering beer.
- Instead of being connected in parallel, as is customary on the market, the membrane modules on the Phoebus are connected in series. As a result, the cross-flow required for filtration can be generated with considerably lower pump output, which not only saves electrical energy but also makes it possible to use smaller-diameter pipes and fittings.
- Shut-off valves between the membrane modules allow the flow direction to be reversed – an advantage that is reflected in a longer filter service life.
- Targeted backflushing of the individual membrane modules increases the effectiveness of cleaning and significantly reduces consumption of cleaning agents and water.
- The membrane modules can be inspected for damage before filtration begins. If a module is found to be defective, it can be automatically excluded from the series and thus by-passed. The defective membrane can be exchanged at a later time.
- The filter line can be operated in continuous or batch mode, as needed. The filtration units can be cleaned individually and then reintegrated into the filtration process.
- The manufacture of the membranes themselves has also been improved. A new process for potting the individual hollow fibers makes it possible to sanitize the membrane modules at a temperature of up to 85 degrees Celsius during operation.
In addition to these Hydronomic UF technologies, the Phoebus also incorporates additional innovations that are perfectly matched to the needs of beer filtration. For example, intelligent control concepts using graduated transmembrane pressures enable the system to respond optimally to the varying filterability of different types of beer. The customary buffer tank for the unfiltrate has also been modified so that it can be used as a sedimentation tank during operation for beers with high yeast loads, to take the pressure off the membrane and prevent excessive yeast concentrations in the cross flow.
Modular design
The filter line features a classic modular design. At a nominal filtration rating of 90 hectoliters per hour, as many as six membrane filter units can be connected in a line. A dedicated CIP system and buffer tanks for absorbing pressure surges round out the system. A single membrane filter unit consists of three membrane packages, which can be arranged in a square or rectangular configuration depending on the space available. The processes are centrally controlled by a PLC (programmable logic control) unit, which can either be provided as a stand-alone solution or integrated into an existing process control system.
After five years in development, the Steinecker Phoebus is now available as a standard product. Ease of use, extremely low beer waste, and the complete elimination of filtration medium make the Phoebus the perfect solution for breweries seeking an alternative to traditional kieselguhr filtration.