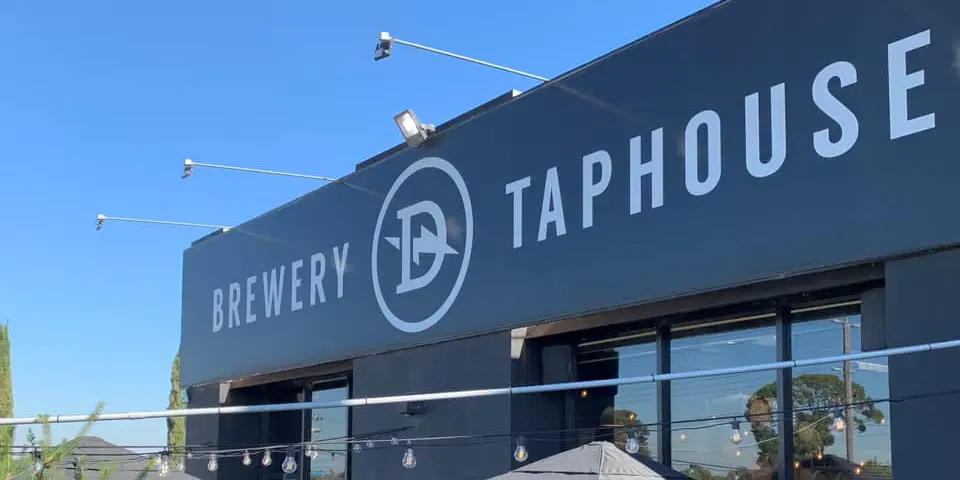
How to start a brewery - part 2
Site Selection & Lease Negotiation
Choose your site to achieve your business plan. There are two common business models, brew and serve on site or brewing for distribution.
- Brewing for serving on site – optimise your brewery site selection for space efficiency, good looks within a venue, serving tanks mounted above fermenters feeding draft dispense system and single batch brewing within a day. Instantaneous hot water systems and two stage (water & glycol) plate heat exchangers can avoid the need for hot and cold liquor tuns, saving capital and space. Key considerations when selecting a site for this business model are:
-
- Site Utilities – is there 3 phase power, mains gas if needed and sufficient
incoming water pressure and flowrate? - Appropriate Zoning – how risky will achieving council approval be?
- Location – will people discover you and continue to return? Is the site close to sporting events, central hubs with good transport links? What and where is the direct competition?
- Car Parking – often a council requirement.
- Ceiling Height – brewing equipment can make good use of this space
- Overall Character and aesthetic of the site – is it an attractive destination?
- Site Utilities – is there 3 phase power, mains gas if needed and sufficient
- Brewing for distribution – design your brewery for low energy costs and high output for every brewing hour, with a 3 or 4 vessel brewhouse configured with thermal stores for daily multi batching. This will reduce the expensive component of labour in each keg of your beer. Double or quad batch fermenters can be installed initially, or at the very least, planned for future expansion by thoughtful glycol system design and adequate space to grow into. It’s important to have adequate space to grow into as growth and sales are a primary focus of this model.
-
- Key considerations for selecting a site for this model are:
- Site utilities, 3 phase power mains gas
- Appropriate zoning, likelihood of council approval
- Multi access points for goods receiving and outgoing
- Floor area for warehouse racking
- Adequate warehouse space for storing finished product coolroom
- Larger floor area to accommodate packaging machinery, grain handling equipment and steam boilers.
- Inexpensive rent
- Suitable existing drainage to minimise flooring costs
Lease negotiation is an important aspect when building your brewery. Some key points to keep in mind when you have found a suitable site and begin discussion with a landlord.
- Is the site fit for purpose? Are there aspects that need improving at the cost of the landlord, clearly identify these and ensure they are fronting the cost.
- Agree to the site with a breakout clause which is dependent on council approval so you are not left with a lease on a site which you are not allowed to use for brewing.
- Is the rent competitive? Are you able to negotiate a lease free period at commencement?
- Is the lease length long enough – 5 year increments with the option of extension is preferrable – are you able to include for the ability to purchase the site in due course?
Council planning, ATO licence and liquor licence
There are three tiers of brewing regulation in Australia:
- Federal ATO excise licence to produce beer – this requires a fit and proper person check on personnel and defines a bonded area within the production facility. Excise must be paid on product that leaves this area or is consumed on site. Calibrated measurement and detailed auditable records must track each step of production and packaging between malt in through to beer out.
- State issued Liquor Licence to sell beer – regulates hours of operation and maximum number of people permitted in the venue.
- Local Council planning permission for use of the land for brewing – considers potential impact on others in the area. As with anything, there is both an easy way and a hard way to achieve the licences and permissions required. They are critical and should be approached with prior education, forethought and respect.
Once a site has been found it’s best to engage a planning consultant who speaks the language of the council and state issued zoning regulation. Together with an architect a formalised site plan and submission can be made to council. Spark provides all the necessary technical file notes and brewery layouts to submit with your planning application making the process collaborative and smooth.
Excise Rebate
From 1 July 2021 the Excise remission scheme for manufacturers of alcoholic beverages (Remission scheme) provides eligible alcohol manufacturers with a full (100 percent) automatic rebate of excise duty, up to a maximum of $350,000 per financial year, on alcoholic beverages they manufacture and enter into the Australian domestic market for home consumption. This full $350,000 rebate level relates to production of approximately 100 kegs per week of 5% ABV beer.
Visit sparkbrew.com to see all the links to the relevant state liquor licence on one page.
Site Preparation
The rule of thirds:
When assessing a potential site it’s good to have an idea of how much space is required for the different aspects of the business. Here is high level breakdown of a typical brewpub site
⅓ = Brewhouse and cellar wet area
⅓ = Dry store and cool room
⅓ = Patron and Service area
A brewery production wet area consists of:
- Well defined wet area that can comfortably fit your chosen equipment as well as any have suitable space to allow for expansion and a comfortable work environment
- The brewery wet area is usually a raised floor with 2% fall to a central strip drain which feeds into a pit. Within the pit is a pump which fills an effluent tank. It’s important to capture all brewery run effluent for treatment.
- The wet area can be surrounded by bund with a splash back or simple plastic bunding, many breweries utilise the bund wall as an opportunity for seating.
- Planning ahead allows easy growth – a glycol ring main extension that includes capped inlet and outlets allows the installation of additional tanks in future.
Brewery Installation
By carefully designing and planning the brewery equipment layout and wet area from the start of the build in collaboration with an architect or builder you can minimise a lot of installation time when equipment arrives on site. Having installed 50 breweries around Australia Spark lead and organise these initial meetings to take the guesswork out of installation for your chosen trades and minimise the cost. That is why every Spark project gets an engineer, brewer and project manager. Some key considerations for minimise the cost and time of installation are:
- Carefully planned layout with utilities map and constructions drawings for the space
- Coordination of equipment delivery with trades and riggers on site
- Careful project management of pre installation tradeworks so as to ensure all work is complete before equipment arrives to site
- Comprehensive debrief with the selected trades and supplemental material to ensure they know exactly what needs to be done
- Installation support so all questions can be answered when they arise
- Long term support to ensure minimal downtime if/ when something goes wrong
Commissioning
Commissioning your new brewing system consists of washing, water brewing and test brewing. The process isolates and tests each element in turn to ensure correct operation before grain is committed to liquor. By allowing the time in your program to do this properly, you ensure the best quality product right from the start. A typical process is:
- Passivation if not already complete – this treats the tanks internal surfaces with strong acid to stop any corrosion forming
- CIP cleaning
- Water brewing – paying close attention to flow sensors and accurate liquor volumes and measuring mash tun dead space, evaporation rate (measuring pre boil volume, post boil volume) measuring total water collected and comparing it to total water initially put into the system. Ensuring you can accurately measure volumes.
- First commissioning run – using the data gathered from the water brew ball park an efficiency of 80 and calculate your recipe – recording total mash water used, total sparge water used, pre boil plato, end of boil plato and total knockout wort collected. This will allow you to dial in your efficiency, equipment losses and evaporation rate. With the aim to remain within .3 plato of your extract target (OG) specification and final ABV.
In our next article, we’ll speak with some breweries to understand their marketing operations and their launch planning, which helped drive them rapidly to profitability.
If you want a long term partner not just an equipment supplier – get in touch.